Pre-Shipment Inspection
A Pre-Shipment Inspection (PSI) is a quality control process that involves a thorough inspection of goods before they are shipped to the customer or buyer. It is carried out to ensure that the products meet the agreed-upon specifications and standards and are fit for their intended use. The goal of PSI is to identify any defects or non-conformities in the product, potentially to rework these prior to dispatch.
The PSI process helps to ensure that the customer receives a high-quality product that meets their requirements and expectations. It also helps to reduce the risk of returns and customer complaints, as well as protecting the reputation of the manufacturer. A PSI is often done prior to paying a balance payment to the vendor so that as a buyer you can feel more confident about the status of the goods that will be shipped.
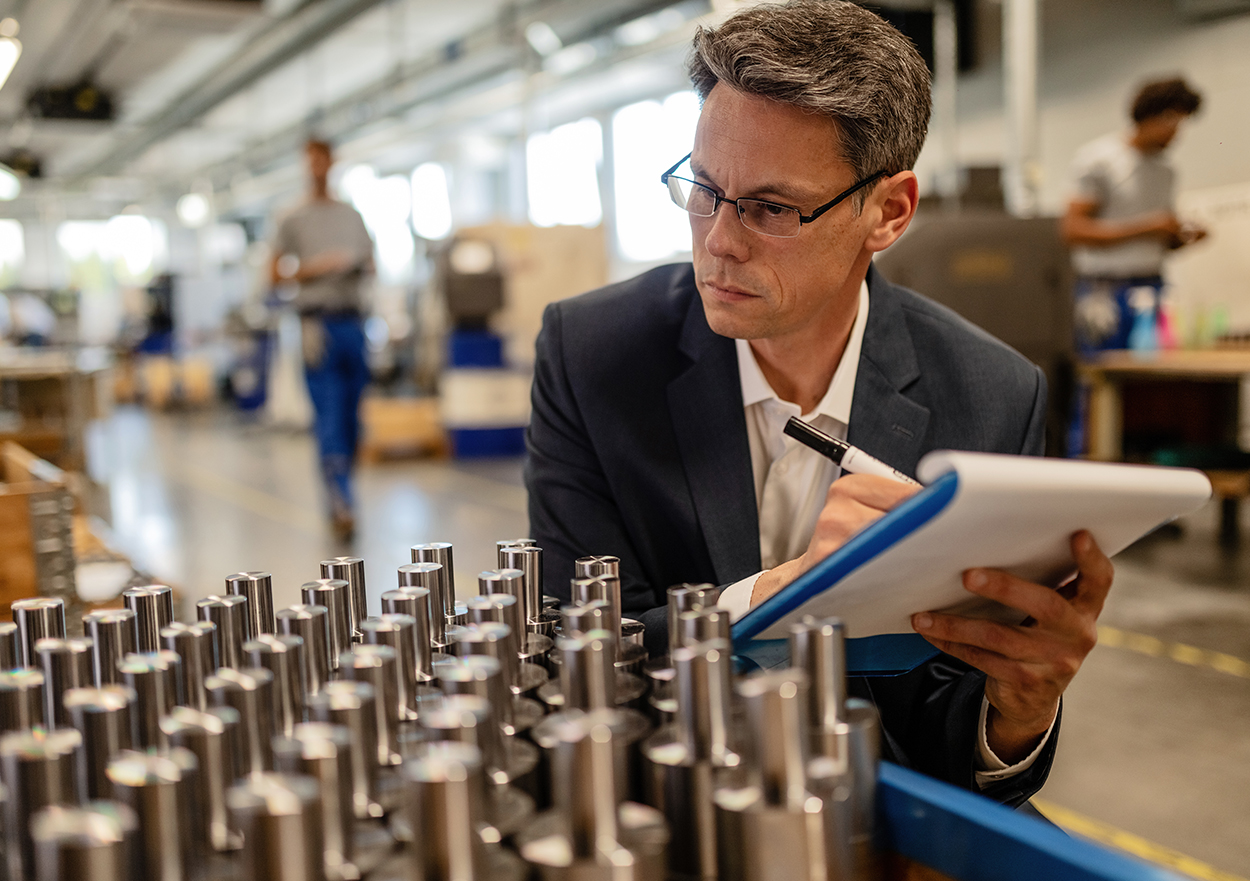
Our Process
The PSI Process follows the following steps:
On-Site Assessment
Inspectors will physically visit the production site or factory to conduct a comprehensive evaluation of your products. This evaluation takes place once the production process is fully completed (100%) and when approximately 80% of your order has been prepared and is ready for shipping.
Quantity Validation
The inspectors will cross-check the quantity of products and their packaging, ensuring that both accuracy and safety for transportation are maintained.
Random Sampling
Employing the Acceptance Quality Limit (AQL) approach, inspectors will randomly choose a subset of products for examination, ensuring statistically reliable results.
Testing for Functionality and Safety
The chosen sample will undergo rigorous tests to ensure proper functionality and adherence to safety standards. This can involve various assessments such as pull tests, fatigue tests, and stretch tests for clothing, along with safety evaluations for electronics and mechanical items.
Evaluation of Appearance and Craftsmanship
Inspectors will physically visit the production site or factory to conduct a comprehensive evaluation of your products. This evaluation takes place once the production process is fully completed (100%) and when approximately 80% of your order has been prepared and is ready for shipping.
Inspection Documentation
Upon completing the inspection, the service provider will furnish you with an in-depth and impartial inspection report. This report will confirm whether the products align with the specifications stated in your Purchase Order (PO) or contractual agreement with the supplier.
Get Quotes and Ensure Quality
Across Your Supply Chain
Contact Info
Our location
Unit 2A, 17/F, Glenealy Tower No 1. Glenealy, Central Hong Kong
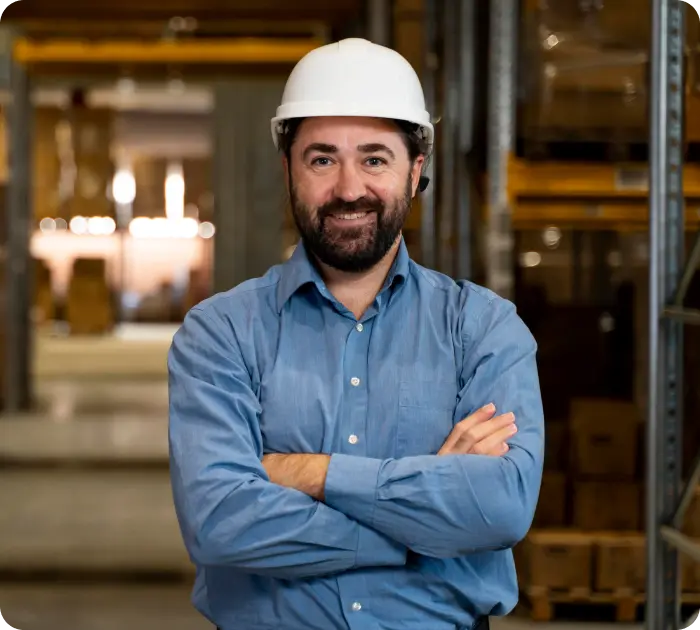