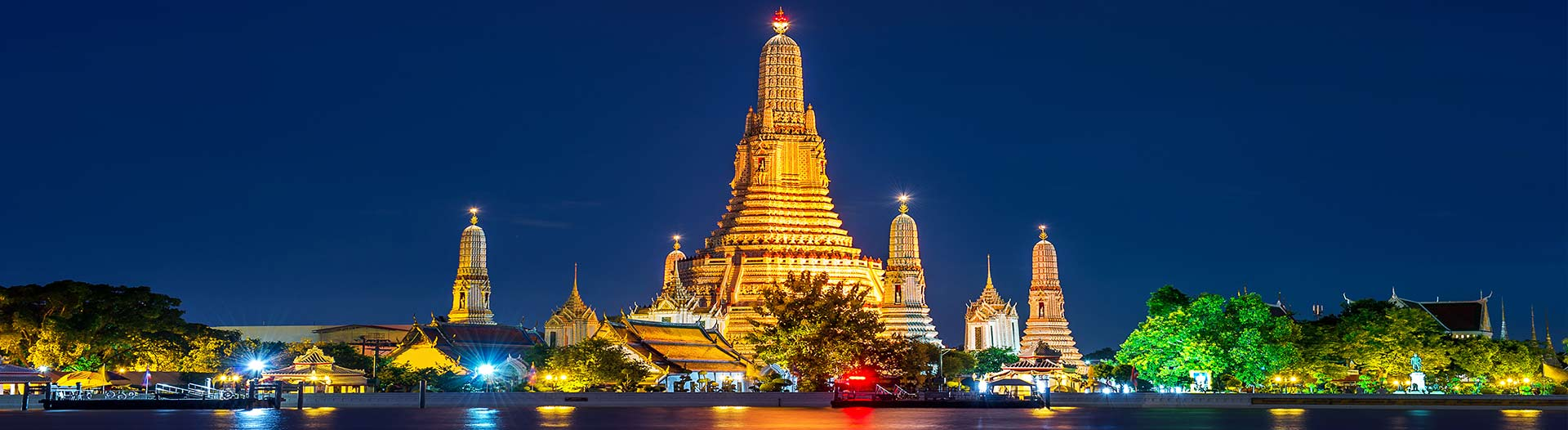
Quality Control & Assurance in Thailand
Quality Control & Assurance in Thailand
Thailand has firmly positioned itself as a leading manufacturing center, catering to a wide spectrum of industries and playing a substantial role in the global export market. Yet, ensuring product excellence and adherence to international standards presents a multifaceted challenge within this dynamic industrial landscape. This is where Thailand’s vital quality control services come into play, providing an extensive array of inspections, audits, and testing procedures to ensure that products align with requisite specifications and global standards.
Thailand’s Diverse Export Product Categories:
Thailand boasts a diverse array of export product categories, bolstering its status as a prominent global exporter. Some notable categories include:
Thailand’s diverse manufacturing and export capabilities have firmly established it as a vital player in the global marketplace.
Product Quality Assurance in Thailand
Ensuring product quality is a paramount consideration at every stage of production in Thailand. This encompasses the evaluation of functionality, performance, appearance, and packaging. Through meticulous inspections, quality control professionals identify defects or deviations from specified standards, ensuring that only high-quality products are delivered to customers.
Supplier & Factory Audits in Thailand
Supplier and factory audits involve comprehensive assessments of manufacturers and suppliers to evaluate their capabilities, quality management systems, compliance with regulations, ethical practices, and more. These audits offer valuable insights into the supplier’s ability to meet the required standards, ensuring reliable and consistent product quality.
Supplier Management Services in Thailand
Supplier management services help importers effectively manage their supplier relationships. These services include supplier performance evaluation, contract management, supplier development, and ongoing monitoring to ensure consistent quality and timely delivery of products.
Product Testing in Thailand
Product testing services in Thailand verify product performance, safety, reliability, and compliance with relevant international standards and regulations. Testing may encompass mechanical, electrical, chemical, and physical evaluations, enabling importers to ensure that their products meet the desired quality and safety requirements.
Common Thai cities with a significant manufacturing presence include:
- Bangkok
- Samut Prakan
- Chonburi
- Rayong
- Nakhon Ratchasima
- Pathum Thani
- Nonthaburi
- Udon Thani
- Khon Kaen
- Chiang Mai
- Hat Yai
- Pak Kret
- Si Racha
- Phra Pradaeng
- Lampang
- Surat Thani
- Ubon Ratchathani
- Nakhon Si Thammarat
- Chiang Rai
- Ratchaburi
In conclusion, quality control services in Thailand play a pivotal role in ensuring product excellence, compliance with international standards, and customer satisfaction. By utilizing a range of inspections, audits, and testing procedures, these services enable importers to mitigate risks, maintain product integrity, and establish reliable supply chains. The presence of numerous manufacturing cities in Thailand underscores the country’s robust manufacturing capabilities and its significant role in the global market. Through the use of quality control services, businesses can confidently source products from Thailand while ensuring consistent quality and adherence to standards.
Get Quotes and Ensure Quality
Across Your Supply Chain
Contact Info
Our location
Unit 2A, 17/F, Glenealy Tower No 1. Glenealy, Central Hong Kong
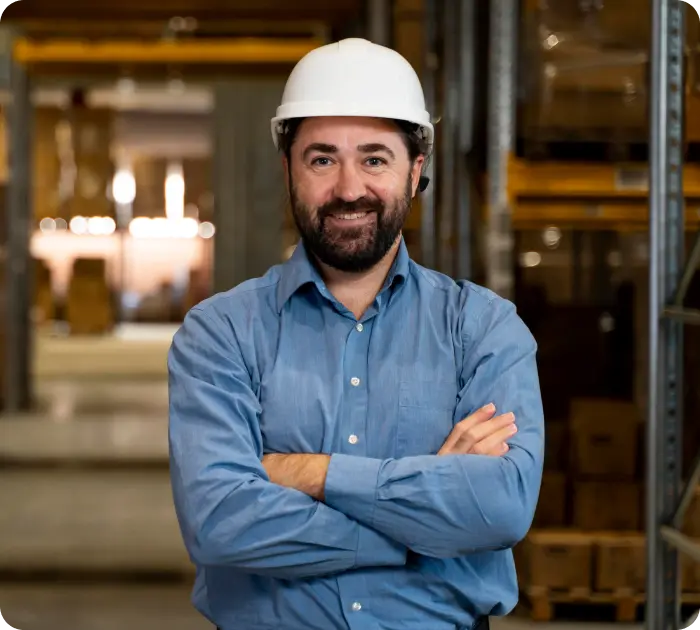