Quality Control in Electronics Manufacturing
Quality control is an essential part of any manufacturing process, but it is particularly crucial in the electronics industry. Electronics manufacturers need to ensure that their products meet high standards of quality, reliability, and safety to meet the demands of their customers and comply with industry regulations. To achieve these goals, manufacturers use a variety of quality control methods, including Statistical Process Control (SPC), Failure Mode and Effects Analysis (FMEA), Six Sigma, Design of Experiments (DOE), and Lean Manufacturing.
Statistical Process Control (SPC)
Statistical Process Control (SPC) is a method that uses statistical analysis to monitor and control a production process. SPC involves collecting data at various points in the production process and analyzing it to identify trends and variations. The goal is to identify when the process is out of control and make necessary adjustments to maintain quality. The key advantage of SPC is that it allows manufacturers to identify problems before they cause defects, which helps prevent product failures and reduces waste.
SPC is particularly useful in electronics manufacturing, where small variations in the production process can have significant effects on the quality and reliability of the final product. By monitoring the process closely, manufacturers can identify when these variations occur and take corrective action to prevent defects.
Failure Mode and Effects Analysis (FMEA)
Failure Mode and Effects Analysis (FMEA) is a systematic approach to identifying and preventing product and process problems before they occur. FMEA involves identifying potential failure modes, determining the severity of the consequences, and developing prevention and mitigation plans. The goal is to identify potential problems early in the development process and prevent them from occurring in the final product.
FMEA is particularly useful in electronics manufacturing, where failures can have serious consequences, such as equipment damage, data loss, or even injury or death. By identifying potential failure modes and taking steps to prevent them, manufacturers can improve the safety and reliability of their products.
Six Sigma
Six Sigma is a data-driven approach to quality control that aims to reduce defects in a production process. The method involves identifying and eliminating the root causes of defects, using statistical analysis and quality tools. The goal is to achieve a defect rate of less than 3.4 defects per million opportunities.
Six Sigma is particularly useful in electronics manufacturing because it can help manufacturers identify and eliminate defects that may not be immediately apparent. For example, defects in the design of a product or in the materials used to manufacture it can have a significant impact on the final product’s quality and reliability. By using Six Sigma methods to identify and eliminate these defects, manufacturers can improve the quality and reliability of their products.
Design of Experiments (DOE)
Design of Experiments (DOE) is a method that involves designing experiments to test the impact of various factors on a production process. DOE can help manufacturers optimize their processes and identify the most effective ways to produce high-quality products. The method involves systematically varying one or more factors in the production process and observing the effect on the final product’s quality.
DOE is particularly useful in electronics manufacturing because it allows manufacturers to test the impact of different process variables on product quality. For example, manufacturers can use DOE to test the effect of different materials or process parameters on the final product’s reliability and performance.
Lean Manufacturing
Lean Manufacturing is a method that aims to eliminate waste and improve efficiency in a production process. Lean Manufacturing involves identifying and eliminating non-value-added activities and implementing continuous improvement processes. The goal is to streamline the production process and reduce waste, while maintaining or improving product quality.
Lean Manufacturing is particularly useful in electronics manufacturing, where waste can have a significant impact on the final product’s cost and quality. By identifying and eliminating waste in the production process, manufacturers can reduce costs and improve the efficiency of their operations while still maintaining or improving product quality. For example, by streamlining the production process and reducing the amount of time it takes to manufacture a product, manufacturers can reduce lead times and improve customer satisfaction.
In conclusion, electronics manufacturers use a variety of quality control methods, including Statistical Process Control (SPC), Failure Mode and Effects Analysis (FMEA), Six Sigma, Design of Experiments (DOE), and Lean Manufacturing, to ensure their products meet high standards of quality, reliability, and safety. These methods allow manufacturers to identify and eliminate problems before they cause defects, optimize their processes to improve efficiency and reduce waste, and continually improve the quality and reliability of their products. By using these methods, electronics manufacturers can meet the demands of their customers and comply with industry regulations while maintaining their competitive edge.
Get Quotes and Ensure Quality
Across Your Supply Chain
Contact Info
Our location
Unit 2A, 17/F, Glenealy Tower No 1. Glenealy, Central Hong Kong
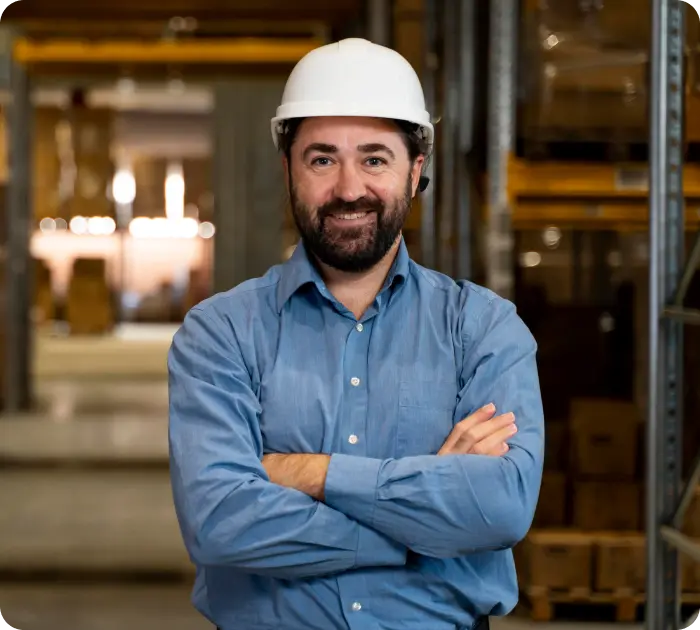