The Difference Between Quality Assurance and Quality Control
Quality control and quality assurance are two critical components of any successful business strategy. Although they may seem similar at first glance, they are, in fact, very different in terms of their objectives, activities, and outcomes. Understanding the differences between these two concepts is crucial for any organization that wants to maximize its efficiency, minimize its costs, and ensure customer satisfaction.
Quality control (QC) and quality assurance (QA) are two approaches to ensuring that products or services meet specified quality standards. While both of these approaches have a similar goal of improving the quality of the final product or service, the ways in which they are achieved are different.
Quality Control (QC)
Quality control (QC) is a set of activities that focus on identifying defects in the product or service. Its primary goal is to identify and correct defects before they reach the customer. The activities involved in quality control include product inspection, testing, and verification. The QC team is responsible for ensuring that the product or service meets the predetermined quality standards.
The QC process is reactive in nature, as it focuses on detecting and correcting problems after they have occurred. The QC team identifies the problems and works to eliminate them so that they do not occur again in the future. The focus of QC is on maintaining consistency in the product or service and ensuring that it meets the specified standards.
Quality Assurance (QA)
Quality assurance (QA) is a set of activities that focus on preventing defects from occurring in the first place. Its primary goal is to improve the overall quality of the product or service by implementing processes and procedures that reduce the likelihood of defects. The activities involved in quality assurance include process monitoring, documentation, and data analysis.
The QA process is proactive in nature, as it focuses on preventing problems before they occur. The QA team works to ensure that the processes and procedures are in place to prevent defects from occurring. The focus of QA is on continuous improvement, by identifying areas for improvement in the process and making changes to ensure that the product or service meets the specified quality standards.
Key Differences between Quality Control and Quality Assurance
- Focus: The primary focus of QC is on identifying and correcting defects in the product or service. The primary focus of QA is on preventing defects from occurring in the first place.
- Reactive vs. Proactive: QC is a reactive process, as it focuses on detecting and correcting problems after they have occurred. QA is a proactive process, as it focuses on preventing problems before they occur.
- Processes and Procedures: QC focuses on ensuring that the product or service meets the specified quality standards. QA focuses on continuous improvement by identifying areas for improvement in the process and making changes to ensure that the product or service meets the specified quality standards.
- Documentation: QC requires documentation of the product or service to ensure that it meets the specified quality standards. QA requires documentation of the process and procedures to ensure that the product or service meets the specified quality standards.
In conclusion, quality control and quality assurance are two different approaches to ensuring that products or services meet specified quality standards. Although they share similar goals, their focus, processes, and outcomes are different. An effective quality management system should incorporate both quality control and quality assurance to ensure that the final product or service meets the specified quality standards, and to continuously improve the processes and procedures.
Get Quotes and Ensure Quality
Across Your Supply Chain
Contact Info
Our location
Unit 2A, 17/F, Glenealy Tower No 1. Glenealy, Central Hong Kong
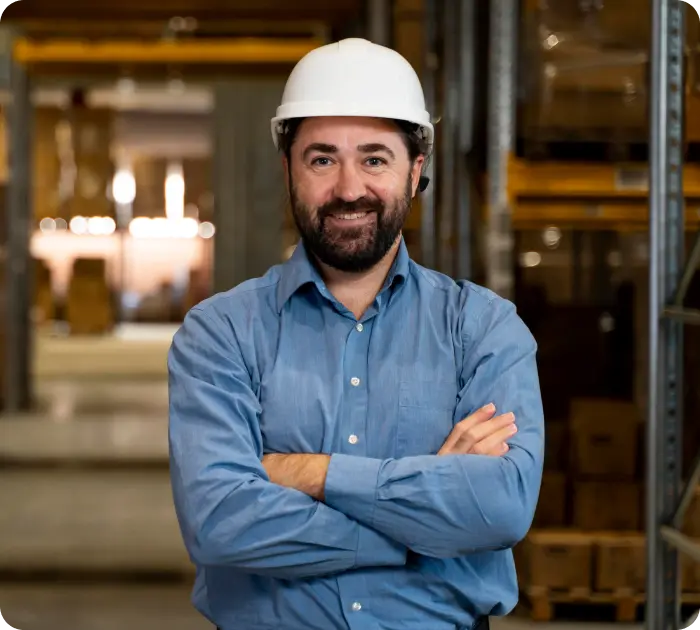