The Imperative of Quality Control in Hardware Production: Avoiding Common Mistakes and Defects
In the realm of hardware production, the pursuit of perfection is an ongoing challenge. From consumer electronics to industrial machinery, the process of manufacturing hardware products is fraught with potential pitfalls and errors that can compromise the integrity and functionality of the final product. Common production mistakes and defects can arise at various stages of the manufacturing process, from design to assembly, testing, and packaging. Understanding these pitfalls and the critical role of quality control is paramount to ensuring the success and reliability of hardware products.
One of the most prevalent issues in hardware production is poor design. Design flaws can lead to a myriad of problems, including compatibility issues, structural weaknesses, and performance limitations. These flaws often stem from inadequate research, rushed development timelines, or a failure to fully understand user needs and expectations. In some cases, design flaws may not become apparent until after the product has been mass-produced, resulting in costly recalls and damage to a company’s reputation. Quality control measures such as thorough design reviews, prototyping, and simulation testing are essential for identifying and rectifying design flaws before they escalate into larger issues.
Another common production mistake is the use of substandard materials or components. Cutting corners on materials can result in products that are prone to premature failure, poor performance, or safety hazards. Whether it’s using inferior metals in structural components, low-quality batteries in electronic devices, or cheap plastics in casings, the consequences of using subpar materials can be severe. Quality control practices such as rigorous supplier vetting, material testing, and incoming inspection procedures are crucial for ensuring that only high-quality materials are used in the production process.
Assembly errors represent yet another significant source of defects in hardware production. Manual assembly processes are inherently prone to human error, ranging from simple mistakes such as incorrect component placement to more complex issues like soldering defects or misalignment of parts. Automated assembly systems can mitigate some of these risks, but they too require meticulous calibration and oversight to ensure consistent and error-free assembly. Implementing robust quality control checkpoints throughout the assembly process, including visual inspections, automated testing, and statistical process control, can help catch and correct assembly errors before they result in defective products reaching the market.
Testing is an integral part of the hardware production process, yet it is often overlooked or inadequately performed. Insufficient testing can result in products with latent defects that only manifest themselves once they are in the hands of consumers. Whether it’s electrical testing for circuit integrity, functional testing to verify proper operation, or environmental testing to assess durability and reliability, thorough testing is essential for identifying and addressing potential issues before they impact end-users. Investing in comprehensive testing protocols and equipment, along with skilled test engineers, is essential for maintaining high standards of quality in hardware production.
Packaging may seem like a minor detail, but it can have a significant impact on the overall quality of a hardware product. Inadequate or improper packaging can result in products being damaged during shipping or storage, leading to returns, warranty claims, and customer dissatisfaction. Quality control measures such as packaging integrity testing, drop testing, and environmental simulation can help ensure that products are adequately protected during transit and storage, minimizing the risk of damage and ensuring a positive out-of-box experience for customers.
In conclusion, quality control is paramount in hardware production to avoid common mistakes and defects that can compromise product integrity and reliability. By implementing robust quality control measures throughout the design, manufacturing, testing, and packaging processes, companies can mitigate risks, minimize costly errors, and deliver hardware products that meet or exceed customer expectations. In today’s competitive market, where reputation and brand loyalty are paramount, investing in quality control is not just a best practice—it’s a business imperative.
Get Quotes and Ensure Quality
Across Your Supply Chain
Contact Info
Our location
Unit 2A, 17/F, Glenealy Tower No 1. Glenealy, Central Hong Kong
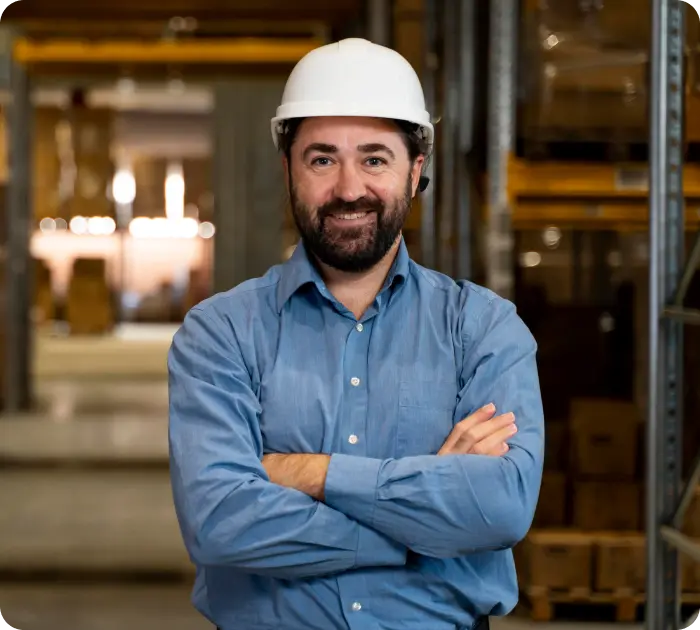